Highlights of ECHT 2024 and the A3TS congress and trade show
The ECHT 2024 European conference, held in conjunction with the 50th A3TS Congress and Exhibition, took place on June 5, 6 and 7, 2024 at the Centre Pierre Baudis in Toulouse, bringing together 1,000 participants from all over the world. The event welcomed 400 delegates, offering 90 conferences on heat and surface treatments around the theme "Flying to a sustainable future", led by international experts. Themes such as sustainability, digitization and industry 4.0 were explored.
The show brought together 80 exhibitors from the materials processing sector, enabling fruitful exchanges, collaborations and new business links. Highlights included two round tables, an innovation competition, a photo contest and job dating.
Technological revolutions: the sustainable future of heat treatment and surface engineering
During the plenary sessions, we were honored to welcome renowned experts to discuss the challenges and technological advances in materials processing, with a particular focus on the aerospace sector and sustainable development.
Mélanie Bedu and Laurent Pinto from Airbus Group (France), presented on the "Challenges of developing metal and surface technologies for a sustainable future", highlighting the strategies and innovations needed to drastically reduce the environmental footprint of air transport.
Thomas Ackerson, Senior Metallurgist at Blue Origin (USA), explored "Materials challenges for reusable hardware and sustainable processes for space travel in the mid-21st century", highlighting needs and potential solutions to make space exploration more sustainable. Marcel Somers from the Technical University (Denmark) discussed "Microstructure optimization in additively manufactured metals by heat treatment and surface engineering", explaining how these techniques can improve the properties of parts produced by 3D printing.
Finally, Denis Descheemaeker, Managing Director of IRT Saint Exupéry (France), detailed IRT ST Exupéry's "Strategy and Technology Roadmap", presenting the institute's plans and initiatives to help develop cutting-edge technologies in the aerospace sector.
Thematic sessions highlighted innovations in heat and surface treatment, focusing on sustainability, digitization and Industry 4.0. Global experts presented advances in sustainable heat treatment techniques, environmentally-friendly alternatives to chromium VI, and process optimization for metallic materials and additives. Collaboration between industry and research is crucial to meeting these technological challenges.
Meet the 80 exhibitors
In parallel with the ECHT2024 Conference, the A3TS Show provided an opportunity for exhibitors and participants to network, discover new technologies and establish future collaborations in the following areas:
Furnaces and Equipment for Thermal Treatment
Equipment for Surface Treatment and Coating
Measurement, Control, Regulation
Services and Processes in Heat Treatment / Surface Treatment
Specialty Chemicals and Consumables
Research, R&D, Consulting
Masterpieces 2024: Olympism in the spotlight
On Wednesday afternoon, June 5, students in the Master 2 Formulation and Surface Treatment (FTS) program at the Université de Franche-Comté received an Olympic-themed trophy for their 2 collaborative projects.
Well done to them!
A3TS 2024 photo competition
The jury, on the theme of "Materials processing in aeronautics", awarded First Prize to Thomas FERNANDEZ for "Le trou d'air.
2nd year student-apprentice in BTS Materials Processing, Lycée Jean Mermoz, St Louis (68).
The aesthetics prize was awarded to Clovis CAILLETON, BTS in materials processing, specializing in heat treatment, Lycée Gaspard Monge de Chambery (59) for "L'espace micrographique".
The technical award went to 1st year students - Master FTS, UFR ST Université de Franche-Comté de Besançon (25) for "L'asticophobie".
Well done to the winners and a big thank you to all the participants and to our partner LAM PLAN for its involvement and contribution to this event.
A3TS 2024 thesis prize
For the first time this year, A3TS organized a French-language thesis prize to encourage and highlight work developing cutting-edge technological knowledge in heat treatment and surface treatment.
Two prizes were awarded to:
- Jérémy Daval for his surface engineering thesis entitled "Elaboration on aluminum substrates of thin, abrasion-resistant and self-lubricating hard anodic layers".
- Miguel Costa Salazar (photo attached) for his heat treatment thesis entitled "The role of nitrogen on phase transformation mechanisms during martensite tempering of steels: experimental approaches and modeling".
The winners presented their work at the exhibition forum and were invited to the ECHT2024 Conference and the 50th A3TS Congress. Our warmest congratulations!
A3TS 2024 innovation trophy awarded to Orano Mining CIME for European ScaVanger project
This project aims to produce scandium sustainably in Europe from by-products of the titanium industry. Used in advanced alloys, scandium is crucial to the aerospace industry, particularly for electric and hydrogen-powered aircraft. The process, developed and validated on an industrial scale, extracts scandium without disrupting TiO2 production. This scandium is then refined for various applications. The initiative supports European autonomy and reduces environmental impact.
-
The European ScaVanger project aims to develop sustainable scandium production in Europe by recovering by-products from the titanium industry. Scandium can be used in advanced alloys for the aeronautics of the future. Orano's CIME, coordinator of the ScaVanger project, is an R&D center that has defined innovative processes and validated them by designing, building and operating industrial-scale pilots at Bessines Sur Gartempe (France).
Question 1: In what context(s) is the innovation intended?
The innovation is aimed at providing lighter, stronger vanadium-containing alloys for the aerospace industry.
Question 2: What level of maturity has the innovation reached? What are the industrial references?
The process has been validated on a pilot scale, and an industrial pilot is currently being designed for industrial demonstration.
Question 3: Explain how innovation can contribute to the industrial performance of its user. What criteria can be used to measure its impact?
Scandium production in Europe will serve the aeronautics industry by enabling the design and manufacture of light, resistant alloys to improve aircraft performance, particularly for electric and hydrogen-powered aircraft, for which weight reduction is essential.
Question 4: Explain the technological content of the innovation. What were the technical challenges? What are the competing solutions/technologies?
The process developed involves connecting a loop directly to an existing flow in the TiO2 production plant, where scandium is present in interesting concentrations. Once the scandium has been extracted, this flow is returned to the plant without disturbing TiO2 production. The extracted scandium is then processed to obtain an intermediate product, scandium hydroxide, with a scandium purity of between 40 and 45%. Depending on market demand and end use, this scandium can be refined to scandium oxide or fluoride with a minimum purity of 99.9%.
The main challenges were not to disrupt existing production by TiO2 producers, and to comply with EU regulations governing this process.
Primary mining projects are under development with Scandium Canada at Crater Lake and Rio Tinto at New South Wells. Scandium is also mined in China (2/3 of current world production). There is no production in Europe.
Question 5: Does innovation contribute to improving the environmental impact of the industrial user?
The aluminum and scandium alloy will help reduce aircraft weight and contribute to the development of electric and hydrogen-powered aircraft. At the same time, it will preserve Europe's total independence of supply. These technologies are ecologically sound and will reduce our impact on the environment.
Contact:
Marine MADEHORS
marine.madehors@orano.group
Four other innovations competed for this award:
-
The traceability of products and their manufacturing processes is becoming increasingly important. Particularly when it comes to components for sensitive applications, or components that are important for safety, complete documentation of processes and parameters is desired, or even required. complete documentation of processes and parameters is desired, or even required. The new "Heat Resistant Barcode" The new "Heat Resistant Barcode" enables complete traceability of heat treatment racks for the first time. of heat treatment racks for the first time. The "Heat Resistant Barcode" is available in several standardized versions, such as base trays, baskets or stacking grids. All barcodes contain both the barcode and the clear number.
Question 1: In what context(s) is innovation envisaged?
Batch traceability for heat treatments
Question 2: What level of maturity has the innovation reached? What are the industrial references?
The product is ready for mass production and the first successful customer applications are already underway.
Question 3: Explain how innovation can contribute to the industrial performance of its user. What criteria can be used to measure its impact?
The use of heat-resistant barcodes enables reliable traceability of loading carriers and thus of heat treatment processes. The "heat-resistant barcode" is applied to load carriers or base trays and baskets, and can be read using commercially available camera scanners.
- high process reliability, ease of use, flexibility of use for different applications, integration into existing systems, automation, simple assembly, low costs, in the event of loss, easy replacement, upgradeability, long service life.
Question 4: Explain the technological content of innovation. What were the technical challenges to be solved? What are the competing solutions/technologies?
The technical challenges were to develop a barcode that could be read by a simple reader, and that could also withstand various heat treatments and hardening. withstand various heat treatments and hardening. We have achieved this with our new development. There is currently no comparable readable product on the market that can be scanned and replaced.
Question 5: Does innovation contribute to improving the environmental impact of the industrial user?
Thanks to batch traceability, environmental impact can be recorded in detail. In fact, all Friedr. Lohmann GmbH Edelstahlgießerei are CO2-neutral. Friedr. Lohmann is the first CO2-neutral stainless steel foundry
-
The PCA 200 portable goniometer from DataPhysics Instruments is a device for measuring surface energy. surface energy. Its main features are as follows:
fast, non-destructive measurement of surface energy on solid surfaces of all sizes
portable, stand-alone device with touch screen for on-site measurements, e.g. in quality control or directly in production processes. quality control or directly in production processes.
automatic determination of surface energy in a matter of seconds and direct display of the result on the device screen. on the device screen.
simultaneous dosing of two drops with the test liquids water and diiodomethane
Question 1: In what context(s) is the innovation planned?
The PCA 200 portable contact angle goniometer is a measuring device designed for quality control processes.
Question 2: What level of maturity has the innovation reached? What are the industrial references?
The PCA 200 was launched in early April 2024.
Question 3: Explain how innovation can contribute to the industrial performance of its user? What criteria can be used to measure its impact?
The PCA 200 enables fast, non-destructive surface energy measurements on solid surfaces of all sizes.
Question 4: Explain the technological content of the innovation. What were the technical challenges? What are the competing solutions/technologies?
Surface energy measurements with the PCA 200 are highly accurate. The PCA 200 can therefore replace the inaccurate test ink measurements still used in many quality control departments.
Question 5: Does innovation contribute to improving the environmental impact of the industrial user? the industrial user?
Yes, because materials with insufficient coating, activation or cleaning treatments can be removed from the product line after the quality control process. and possibly reprocessed before being sent to customers. In this way, companies can reduce their return rates and guarantee consistently high product quality.
-
The current treatment uses pulses of C2H2 and NH3 to enrich the surface of a 23MnCrMo5 steel with interstitial elements (i.e. carbon and nitrogen). 23MnCrMo5 with interstitial elements (i.e. carbon and nitrogen). The number of pulses, time, pressure and temperatures were chosen so as to obtain 60% austenite (by volume) near the surface, with a limited amount of CrNo5. and Fe3C. It was measured that, after tempering and shot peening, such a high fraction of austenite was obtained near the surface, this high fraction of austenite improved fatigue and impact properties.
Question 1: In what context(s) is innovation envisaged?
This new carbonitriding treatment has been developed to improve the service life of gears used in the automotive industry. the automotive industry. Service life is mainly controlled by wear due to fatigue and impact.
We developed a carbonitriding treatment based on pulses of C2H2 and NH3. The treatment consisted of 6 pulses of NH3 and 27 pulses of C2H2, with N2 gas quenching at room temperature as the final step. The treatment lasted 3 hours and 10 minutes. The aim was to maintain a very high austenite fraction near the surface of the treated parts. The visual shows the microstructure of a 23MnCrMo5 carbo-nitrided steel, treated under the conditions listed above, so as to retain 60% austenite (bright phase). This austenite is thought to be beneficial for fatigue and impact properties (see Question 3).
In general, it is not easy to maintain such high austenite fractions. The corresponding hardness profile is illustrated: the drop in hardness near the surface, due to a high austenite fraction, is desired.
After tempering and subsequent shot peening, the deformation-induced transformation of austenite into martensite was observed (TRIP effect), which explains the shape of the resulting microhardness profile.
Question 2: What level of maturity has the innovation reached? What are the industrial references?
The technological maturity level is TRL 6-7. Prototype treatment was carried out in industrial carbonitriding equipment, which is considered an "operating environment" for most manufacturers. Mechanical characterizations were carried out on coupons dedicated to impact and 4-point bending, and may need to be verified on real gears to reach a higher TRL.
Question 3: Explain how innovation can contribute to the industrial performance of its user.
Carbonitriding is important for improving the service life of gears exposed to wear and fatigue. It has been shown that, compared with conventional carbonitriding treatment (typically 15-20% austenite), our current treatment improves :
4-point bending fatigue limit of 5 to 6%.
the maximum load for Brugger tests by 8%. NB: The Brugger test is an alternative to the Charpy impact test, as the Brugger test is better suited to gears.
For more details, see C. Depredurand's presentation [1]. [1] C. Depredurand (CETIM), D. Maréchal (IRT M2P), J. Dulcy (IRT M2P), A. Philippot (Ascometal), "Characterisation of a low-pressure carbonitriding treatment with a high retained austenite content", presentation on 05/06/2024 | A3TS |Toulouse.
Question 4: Explain the technological content of the innovation. What were the technical challenges? What are the competing solutions/technologies?
The use of low-pressure mode and N2 gas quenching make it difficult to adjust the austenite volume fraction. In order to control the austenite fraction, we have modeled the diffusion profiles of carbon and nitrogen in the austenite. This numerical work was presented last year at the A3TS/ECHT congress (July 2023 - Mulhouse) [2].
Another challenge is the formation of block cementite, which can be detrimental to fatigue properties. Usually, one solution is to grind the surface to remove the cementite, but with the risk of removing the desired austenite-rich layer. Our innovation allows only small spheroids of cementite (generally beneficial for fatigue) to be formed, but no block cementite, so no further grinding is required.
[2] D. Maréchal, J. Dulcy, J. Valette, M.-R. Chini, "Simulations thermodynamiques pour optimiser les gammes de traitements thermochimiques Basse Pression", presentation given on 05/07/2023 | A3TS / ECHT 2023 | Mulhouse.
Question 5: Does innovation contribute to improving the environmental impact of the industrial company?
In addition to extending the service life of gears undergoing the current treatment, we have sought to design an eco-responsible treatment. eco-responsible treatment.
The use of a low-pressure process means that little gas (C2H2 or NH3) is consumed, which significantly reduces the direct emissions associated with the process. which significantly reduces the direct emissions associated with the process. In addition, we have taken care to :
- use only the minimum amount of gas required for the treatment.
- to keep treatment times to a minimum.
For grade 23MnCrMo5 enriched under our conditions, N2 gas quenching achieves sufficient hardenability. gas N2. From an environmental point of view, gas quenching is more attractive than oil quenching, as it avoids the negative effects of gas quenching on the environment. oil quenching, as it avoids the negative effects of oil quenching on the environment.
- the need to produce mineral oil,
- the additional degreasing process after quenching.
-
Laser powder bed fusion (L-PBF) is gradually finding its way into many industrial applications. While this technology is making considerable progress, enabling the production of parts of ever-increasing quality, surface quality requirements are becoming increasingly stringent. Roughnesses in the micron range are now expected in certain industrial specifications. To meet this requirement, a new generation of chemical polishing baths has been developed as part of the NEMO project supported by IRT M2P. The results obtained on TA6V parts enable sub-micron roughness values to be obtained.
Question 1: In what context(s) is innovation envisaged?
This innovation comes in the context of surface finishing of titanium parts manufactured by additive manufacturing (L-PBF) L-PBF: roughness reduction and removal of unmelted surface particles.
Question 2: What level of maturity has the innovation reached? What are the industrial references?
This innovation is currently operating at 70L scale, and is being applied to industrial titanium parts and demonstrators from various industrial fields. demonstrators from various industrial fields.
Question 3: Explain how innovation can contribute to the industrial performance of its user. What criteria can be used to measure its impact?
This new bath enables very low roughness values to be achieved, in line with manufacturers' increasingly stringent specifications. It also benefits from the advantages offered by chemical processes in terms of accessibility to the interior of complex parts.
Question 4: Explain the technological content of the innovation. What were the technical challenges? What are the competing solutions/technologies?
The main challenge in developing this innovation was to optimize the competition between surface dissolution reactions and species diffusion towards the surface, in order to maximize roughness reduction while minimizing material removal. This new bath competes with chemical machining baths, which also enable roughness to be attacked, but with greater material removal. More generally, this process also competes with all surface finishing processes (chemical, electrochemical, mechanical, etc.).
Question 5: Does innovation contribute to improving the environmental impact of the industrial company?
Thanks to its performance, this process achieves the desired surface finish in a single step, which is an advantage in terms of environmental impact. In addition, regeneration solutions are currently being developed to minimize the environmental footprint of the process.
Technological revolutions and environmental challenges: ECHT 2024's flagship roundtables
Two round tables were held at the show on June 6. In the morning, the "Low-carbon aircraft of the future" round table brought together Wolfgang Brochard (AIRBUS), Sandrine Bozzi (Aubert & Duval), Olivier Delcourt (Safran), and Denis Descheemaeker (IRT Saint-Exupéry) to discuss the innovations needed to reduce the carbon footprint of aircraft.
In the afternoon, the round table on "The stakes of PFAS limitations for the mechanical and electrical industries" brought together Aurélie Clair (Michelin), Guillaume Desbordes (CITRA), Hélène Ierno-Rochais (Safran), Anne-Sophie Maze (UITS), Jaouad Salmi (IREIS HEF Group), and Pierre Henrard (IRT Saint-Exupéry) to explore the impacts of new regulations and alternative solutions.
Find press articles:
La Tribune Toulouse - June 8, 2024
La Tribune Toulouse - June 18, 2024
Job Dating
On Thursday morning, June 6, job dating took place at the show. Numerous candidates were able to meet the exhibitors present.
All the players and companies had meetings with quality candidates, enabling them to consider recruiting and potential collaborators.
An exceptional evening at the Aeroscopia Museum: awards and high-flying entertainment!
The gala evening organized at the Aeroscopia museum in Blagnac was a resounding success, attracting almost 380 participants. Guests were able to admire the rich aeronautical collection and visit emblematic aircraft such as the Concorde, A380, Super Guppy and A300B. Cocktails were served on the tarmac, and dinner was served at the foot of the aircraft. The A3TS 50th anniversary quiz, hosted by Sylvain Batbedat and Olivier Delcourt, was won by two top-flight tables. A TOP GUN photobooth left everyone with memorable souvenirs.
Finally, two honorary titles were awarded during the evening: Pierre Bruchet was named Honorary President for his decisive actions in the service of the association over almost 20 years, and René Mauvoisin received the title of Honorary Member for his great services to the A3TS in the field of training.


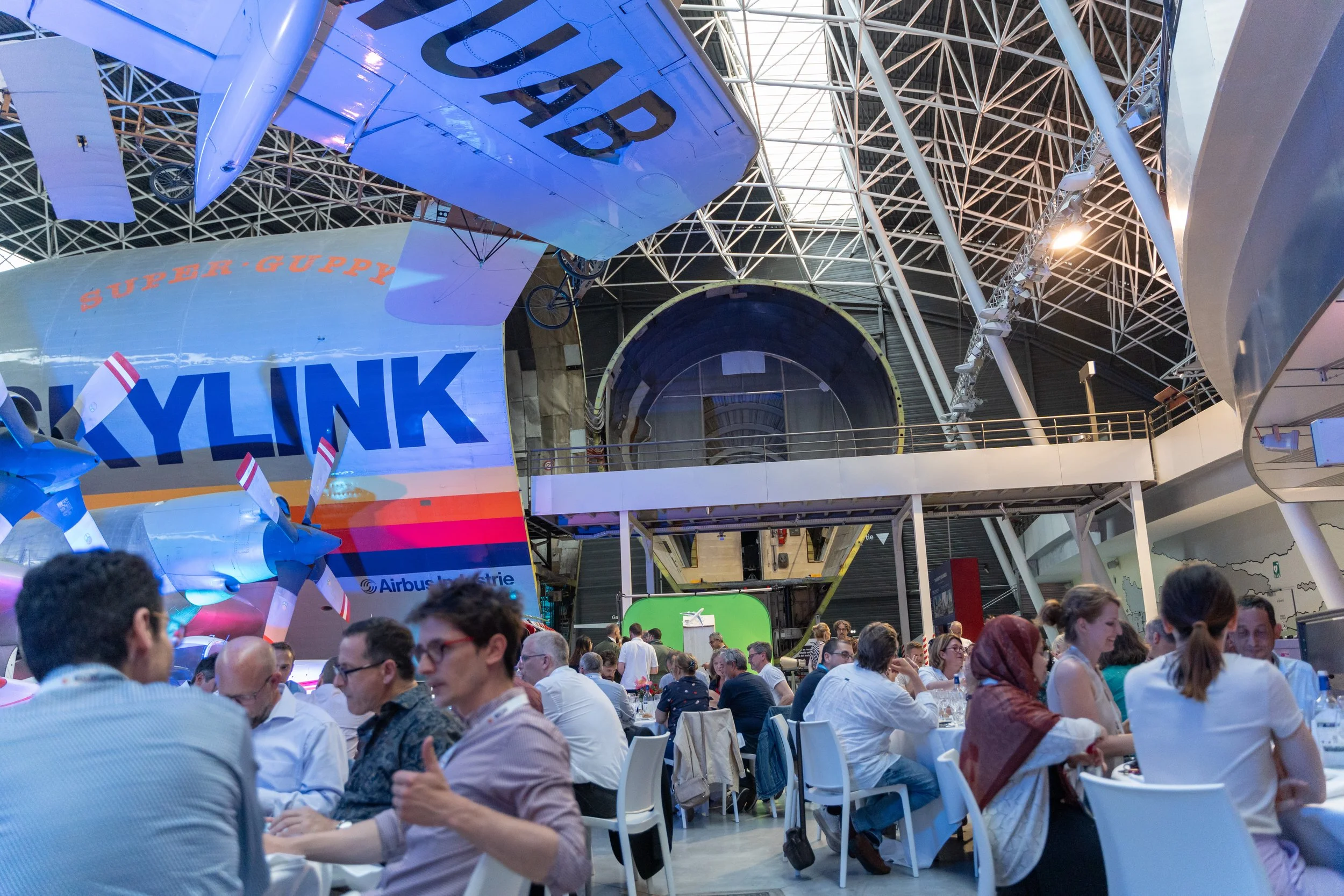



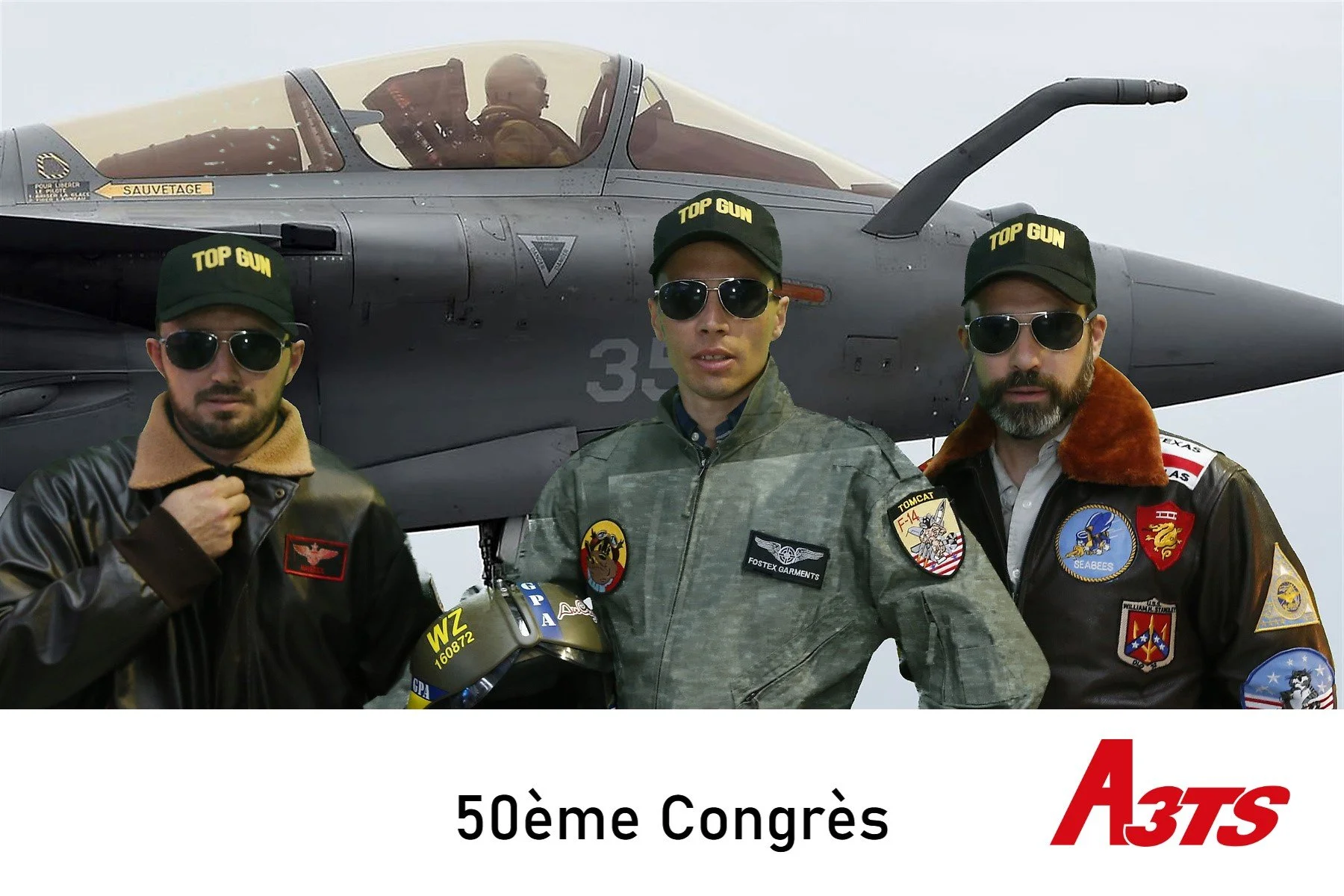

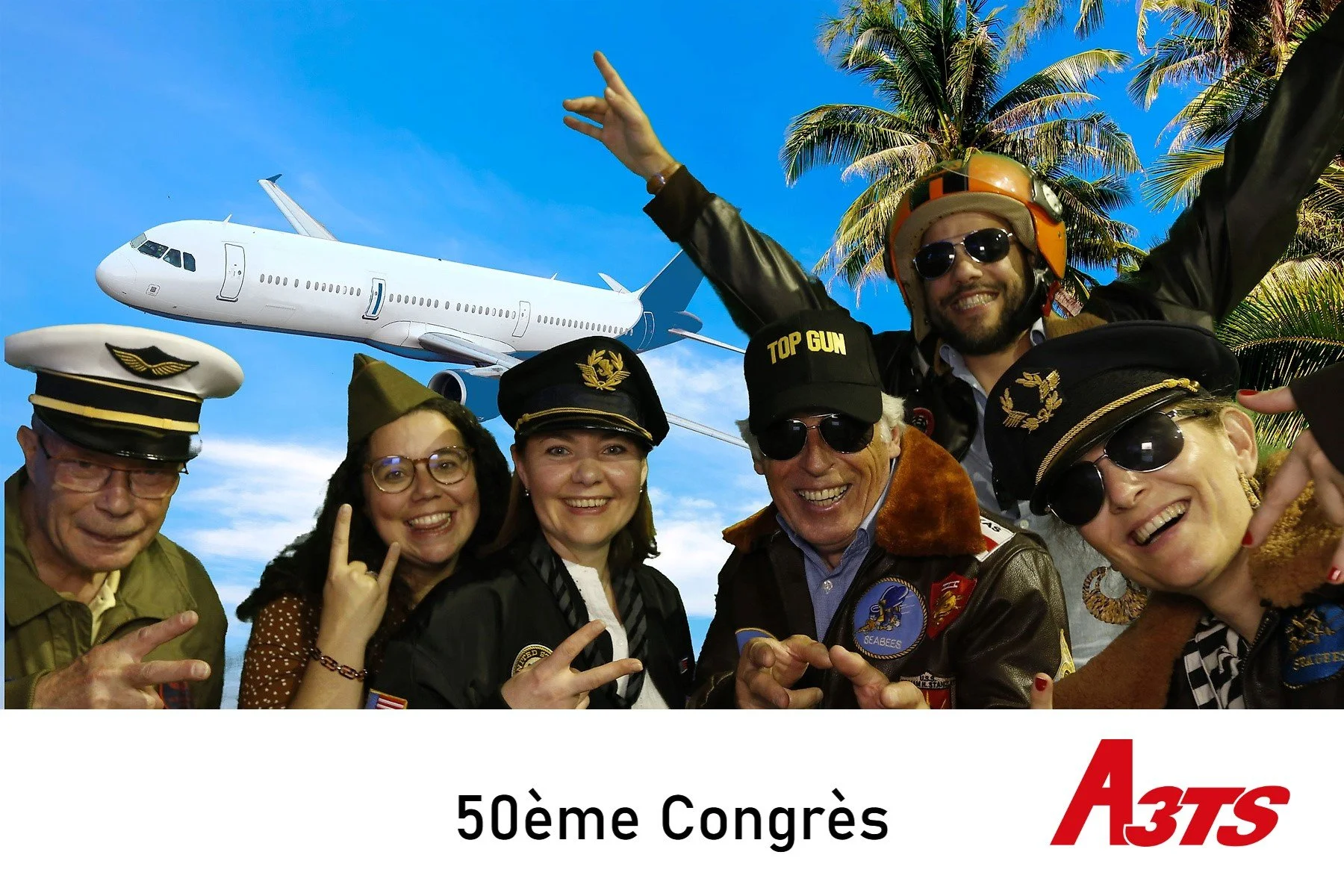